Introduction
Surface finishes in CNC machining are crucial for enhancing the appearance, functionality, and durability of machined parts. From automotive components to custom jewelry, the right finish can significantly influence the performance and aesthetic of the product.
Understanding Surface Finishes
Surface finishes in CNC machining involve various techniques that alter the surface of a machined part to achieve desired properties:

Anodizing: This process enhances corrosion and wear resistance, makes the surface non-conductive, and can be dyed in various colors. Type II anodizing is common for aesthetic purposes, while Type III provides a hard, durable surface suitable for rugged environments (3ERP) (Protolabs Network).
Powder Coating: Offers a thick, wear-resistant layer that improves durability and aesthetics. It's applied as a dry powder and then cured under heat, providing a uniform finish that's tougher than conventional paint (xcmachining.com).

Electroplating: Adds a thin layer of metal to the surface, enhancing appearance and corrosion resistance. It's particularly useful for decorative finishes or when electrical conductivity is required (rapiddirect).
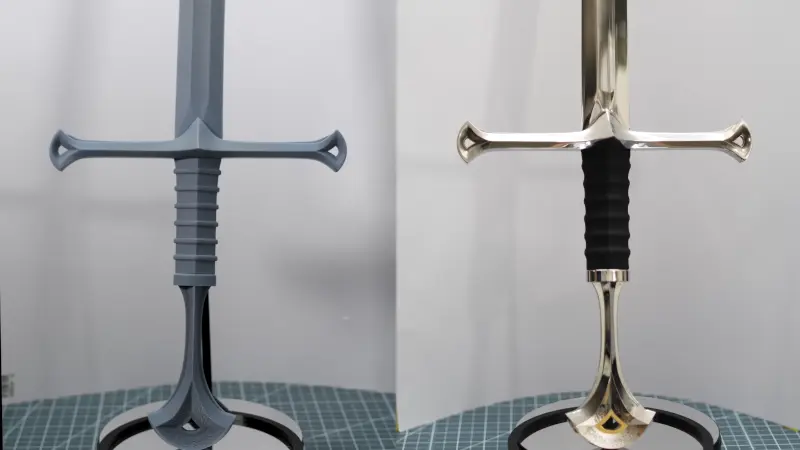
Bead Blasting: This method creates a uniform matte or satin finish by bombarding the surface with glass beads, which helps to mask machining marks and minor surface imperfections (xcmachining.com) (American Micro Inc.).

Advanced Techniques
Laser Engraving: Used for detailed marking or decorative designs, laser engraving offers precision without compromising the part's structural integrity (3ERP).
Heat Treating: Various methods like annealing, tempering, and case hardening enhance the mechanical properties of the machined parts, such as strength and durability (3ERP).
Choosing the Right Finish
Selecting the appropriate finish depends on several factors, including material type, intended application, and required aesthetic or functional properties. For instance, anodizing is suitable for aluminum and titanium, while powder coating works well on a variety of metals (Staub Precision Machine, Inc.). Each finish brings its own set of advantages, such as improving wear resistance, reducing friction, or enhancing appearance.
Implementing Surface Finishes
The application of surface finishes involves careful planning and execution. Proper preparation, such as cleaning and deburring, is crucial before applying any finish to ensure optimal adhesion and effect (Staub Precision Machine, Inc.). The choice of finishing technique impacts not only the product’s performance but also its manufacturing costs and production timeline.
Conclusion
Understanding and applying the correct surface finishes in CNC machining is essential for producing high-quality parts that meet specific functional and aesthetic criteria. By integrating these finishing techniques, manufacturers can enhance the durability, appearance, and performance of their CNC machined parts.
コメント