Exploring CNC Machining Techniques: Milling, Turning, and Drilling
- Calvin Wu
- Apr 27, 2023
- 3 min read
Outline:
A. Overview of CNC machining
B. Importance of milling, turning, and drilling techniques
C. Purpose of the blog post
A. Definition and basic principles
B. Types of milling machines
C. Cutting tools and toolpaths
D. Advantages and limitations

A. Definition and basic principles
B. Types of turning machines (lathes)
C. Cutting tools and toolpaths
D. Advantages and limitations

A. Definition and basic principles
B. Types of drilling machines
C. Cutting tools and toolpaths
D. Advantages and limitations
A. Application suitability
B. Material compatibility
C. Surface finish capabilities
D. Production efficiency
A. The importance of understanding CNC machining techniques
B. The role of manufacturers and designers in selecting the appropriate technique for specific applications
INTRODUCTION
CNC (Computer Numerical Control) machining is a versatile manufacturing process that utilizes computer-controlled machines to create intricate, precise parts. Milling, turning, and drilling are three primary CNC machining techniques that form the foundation of this process. This blog post explores these techniques, discussing their principles, advantages, and limitations, and offering insights into their various applications.
CNC MILLING
CNC milling is a machining process where a rotating cutting tool removes material from a workpiece. The cutting tool follows a predetermined toolpath, guided by computer-aided design (CAD) and computer-aided manufacturing (CAM) software.
Milling machines come in various configurations, including vertical and horizontal mills, which differ in their spindle orientation. Cutting tools used in milling vary in shape and size, depending on the desired geometry and surface finish.
Advantages of CNC milling include the ability to produce complex geometries and high precision. However, limitations include potential difficulties in machining certain materials and increased setup time for complex parts.

CNC TURNING
CNC turning is a machining process where a workpiece is rotated about its axis while a stationary cutting tool removes material. Like milling, turning operations are guided by CAD and CAM software to create precise geometries.
Turning machines, or lathes, come in various configurations, including horizontal and vertical lathes, turret lathes, and Swiss-type lathes. Cutting tools for turning operations are designed to shape and contour the workpiece as it rotates.
Advantages of CNC turning include high precision, fast production rates, and the ability to produce cylindrical parts. Limitations include restrictions in part geometry and difficulties in machining non-cylindrical features.
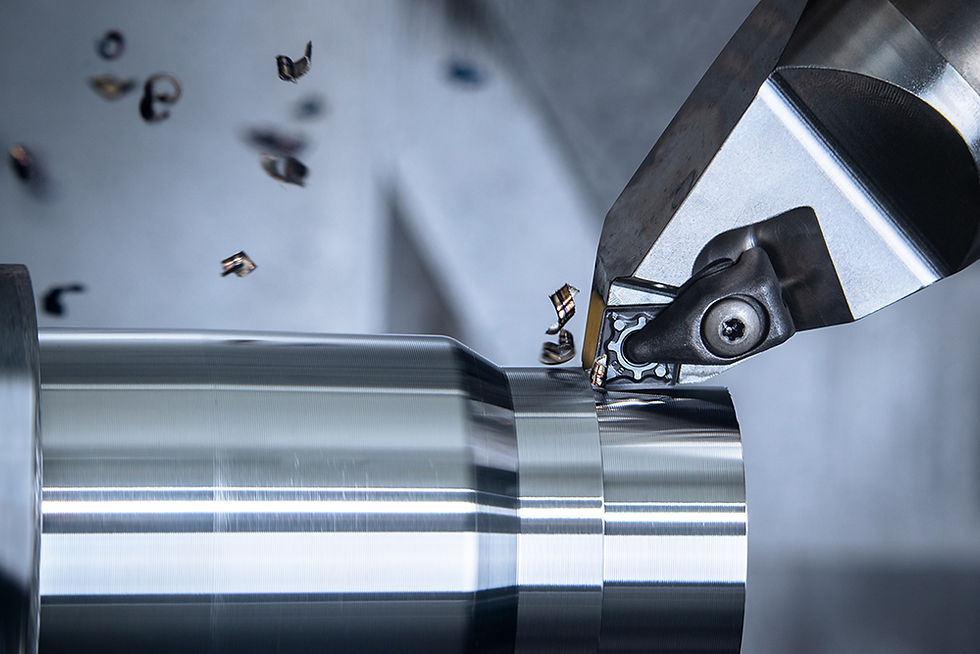
CNC DRILLING
CNC drilling is a machining process that uses a rotating cutting tool, typically a drill bit, to create holes in a workpiece. As with milling and turning, drilling operations rely on CAD and CAM software for toolpath guidance.
Drilling machines come in various types, such as vertical drilling machines, horizontal drilling machines, and radial drilling machines. Cutting tools used in drilling operations vary in diameter, material, and geometry to accommodate different hole sizes and workpiece materials.
Advantages of CNC drilling include high precision, rapid hole production, and the ability to create holes in various materials. Limitations include restrictions in hole geometry and potential difficulties in drilling deep holes or angled holes.
COMPARING MILLING, TURNING, AND DRILLING
When comparing milling, turning, and drilling, consider the following factors:
Application suitability: Choose the technique that best suits the part's geometry and required features. Milling is ideal for complex geometries, turning for cylindrical parts, and drilling for hole creation.
Material compatibility: Each technique has different capabilities in terms of material machinability, so consider the workpiece material when selecting a machining process.
Surface finish capabilities: Different techniques produce varying surface finishes. Milling and turning can achieve a wide range of surface finishes, while drilling is primarily focused on hole creation.
Production efficiency: Consider the production rate and setup time of each technique to optimize production efficiency.
CONCLUSION
Understanding the fundamentals of CNC machining techniques, specifically milling, turning, and drilling, is essential for selecting the most appropriate process to create high-quality, precise parts. By considering factors such as application suitability, material compatibility, surface finish capabilities, and production efficiency, manufacturers and designers can make informed decisions and optimize their machining processes.
Comentarios