High-Speed CNC Machining: Techniques and Benefits
- Calvin Wu
- Apr 4, 2023
- 1 min read
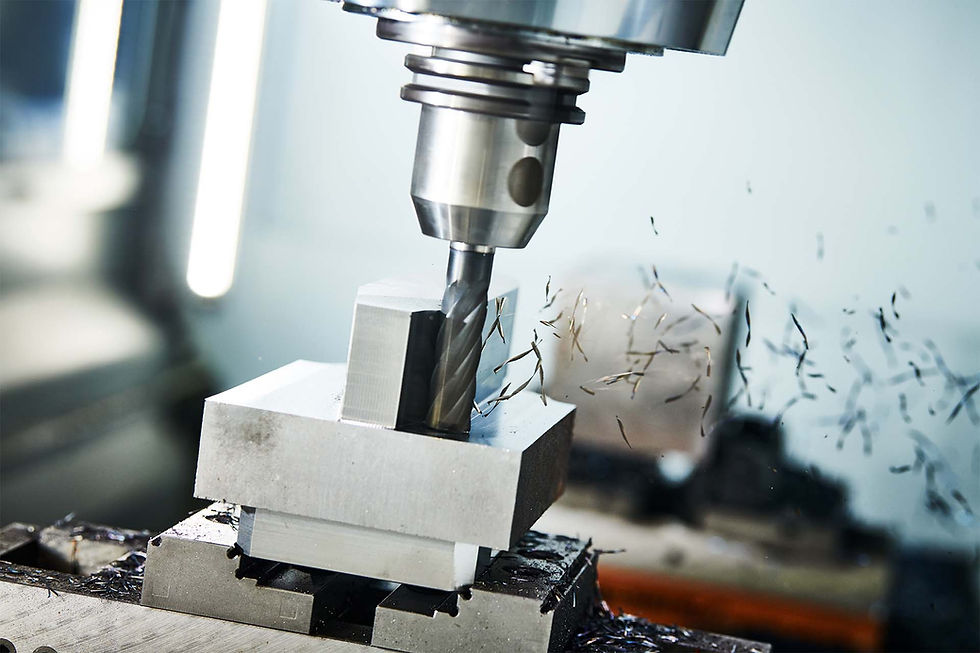
High-speed machining (HSM) is an advanced milling process that involves fast, light cuts instead of slow, heavy ones. It offers increased efficiency, accuracy, and surface finish by leveraging high cutting speeds, high spindle speeds, high feed rates, and high removal rates. This method has evolved with the development of advanced CAD/CAM software and CNC machines, making it more accessible for modern manufacturing.
Benefits of high-speed CNC machining include:

Improved accuracy and surface finish compared to conventional milling.
Increased material removal rate, leading to shorter production times.
Reduced tool wear and longer tool life.
Enhanced machining of thin-walled features and complex geometries.
Key tools and techniques for high-speed CNC machining include:
Dedicated roughing and finishing tools for reduced wear.
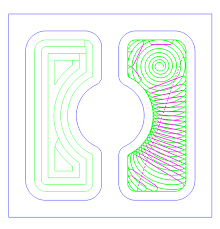
Short, rigid tooling for better accuracy and surface finish.
Balanced tooling and shrink fit tooling for stability at high RPMs.
Effective chip management using oil mist, air blast, or coolant.
Trochoidal machining, plunge roughing, radial chip thinning, side steps, cornering, smart machining, and knowledge of stock remaining for optimal toolpath generation and machining efficiency.
In conclusion, high-speed CNC machining provides significant advantages over conventional milling, enabling faster production times, better accuracy, and improved surface finishes. By employing dedicated tools and advanced techniques, HSM can dramatically enhance the manufacturing process across various industries.

Comments